When it comes to the backbone of modern construction and manufacturing, bolts are an essential component. From bridges to automobiles and heavy machinery, bolts provide the necessary strength and reliability to hold critical structures together. But how are bolts made? What role do bolt molds play? This blog post delves into the bolt manufacturing process and highlights the pivotal function of molds (dies) in ensuring precision, efficiency, and durability.
What Is a Bolt?
A bolt is a type of threaded fastener designed to be used in conjunction with a nut to hold objects together. It typically consists of two main parts: the head and the shank, which is usually partially or fully threaded. Bolts are manufactured in a variety of shapes, sizes, and materials, depending on the application, including carbon steel, stainless steel, and alloy steel.
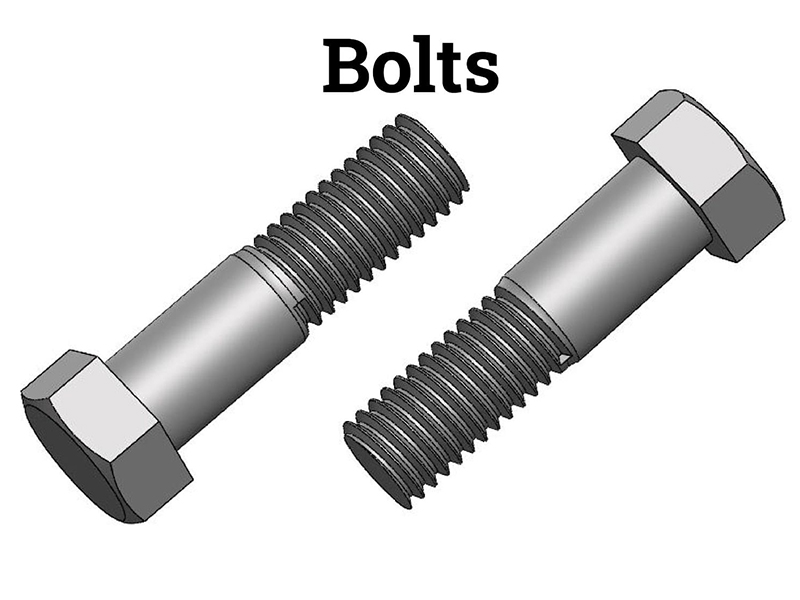
Now let’s break down how bolts are made, step by step.
Step-by-Step: How Are Bolts Made?
1. Raw Material Preparation
The bolt manufacturing process starts with selecting the appropriate raw material, usually coiled steel wire rod. This steel wire is cleaned through acid pickling and then coated with a lubricant (phosphate or soap) to prepare it for the forming process.
2. Cutting to Length (Cold Heading Preparation)
The steel wire is drawn through a series of dies to reduce its diameter to the required size and then cut into appropriate lengths. These cut pieces are called blanks, which are ready for heading and threading.
3. Cold Heading / Hot Forging (Forming the Bolt Head)
One of the most critical stages in bolt production is cold heading or hot forging. During this stage, the bolt blank is placed into a heading machine, where it's formed into the desired head shape — hexagonal, square, or other custom designs.
Cold heading is used for small to medium-sized bolts and involves reshaping the metal at room temperature using bolt molds (dies).
Hot forging is used for large bolts and involves heating the blank before forming.
Here, bolt molds are crucial. They consist of a punch and a die, which work together under high pressure to shape the head of the bolt with precision.
4. Trimming (Optional)
If excess material remains around the bolt head after forging, it’s trimmed using specialized tools to ensure a clean and uniform shape.
5. Thread Rolling
After the head is formed, the next step is thread rolling. This process does not cut the threads but rather forms them by pressing the blank between two dies—a stationary die and a moving die. This enhances the bolt’s tensile strength because the metal is not cut but deformed into threads, maintaining grain flow.
The dies used here are another type of bolt mold specifically designed for precision thread formation. The design and quality of these dies directly affect the accuracy and durability of the bolt threads.
6. Heat Treatment
Depending on the application, bolts may undergo heat treatment (such as quenching and tempering) to improve mechanical properties like hardness, strength, and ductility.
7. Surface Finishing
Surface treatments like zinc plating, galvanizing, black oxide, or phosphate coating are applied for corrosion resistance and improved appearance.
8. Inspection and Quality Control
Each batch of bolts is subjected to strict quality inspections, including dimensional checks, tensile strength tests, and thread accuracy verification, ensuring compliance with international standards like ISO, DIN, or ASTM.
What Role Do Bolt Molds Play?
Bolt molds — commonly known in the industry as dies and punches — are the heart of the bolt manufacturing process. They are precision-engineered tools responsible for forming the bolt head and threading the shank. Here's a deeper look into their role:
1. Precision Forming
Bolt molds define the shape and size of the bolt head. They ensure that each bolt produced meets exact dimensional specifications, which is vital for consistent assembly performance across large-scale industrial applications.
2. Material Efficiency
High-quality molds allow for cold forming of bolts, a method that reduces material waste and improves efficiency. Unlike machining, cold heading and rolling do not remove material but reshape it — a more sustainable and cost-effective approach.
3. Tool Longevity and Cost-Effectiveness
Durable bolt molds made from high-speed steel or tungsten carbide can withstand the extreme pressures of high-volume production. This translates to longer tool life, reduced downtime, and lower maintenance costs — key factors in competitive manufacturing environments.
4. Customization
Industries often require custom bolt designs, whether for aerospace, automotive, or infrastructure. Custom molds enable manufacturers to produce specialized bolt heads or threads, meeting exact customer requirements without compromising quality.
5. Thread Accuracy and Strength
The threading dies in bolt molds form high-precision threads that are stronger than cut threads due to improved grain flow. This contributes to better load distribution and higher resistance to fatigue and wear.
Conclusion
Bolts are manufactured through a combination of wire drawing, cutting, cold heading or hot forging, thread rolling, heat treatment, and surface finishing.
Throughout this process, bolt molds (dies and punches) are indispensable tools that ensure precision, consistency, and strength in the finished product.
In the competitive fastener manufacturing industry, the quality of the bolt molds directly affects production efficiency, product durability, and ultimately, customer satisfaction. Whether you're producing standard bolts or custom fasteners, investing in high-performance molds is critical to maintaining excellence and staying ahead in the market.
For more insights into the fastener mold industry or to consult on your specific requirements, feel free to contact us — your expert partner in bolt mold solutions.