Cold forging is a precision manufacturing process that requires robust, reliable tooling to produce high-quality components. One of the key elements in ensuring success in cold forging operations is the selection of the optimal cold forging die material. In this comprehensive guide, we delve into the properties, selection criteria, and best practices for choosing cold forging die materials that not only extend tool life but also boost productivity and product quality.
Understanding Cold Forging
Cold forging, also known as cold forming, is a process where metal is shaped at or near room temperature using high-pressure forces. Unlike hot forging, which involves elevated temperatures, cold forging preserves the metal's inherent strength, improves surface finish, and results in parts with superior dimensional accuracy. However, these benefits come with the challenge of higher stresses on the tooling.
The durability and performance of the die heavily depend on the chosen cold forging die material. A well-selected material will endure repeated impacts and high-pressure cycles while maintaining precision, which is critical for achieving tight tolerances in finished products.
Why Cold Forging Die Material Is Crucial
Die materials directly influence the efficiency and consistency of cold forging operations. Some key reasons why the right cold forging die material matters include:
Tool Life and Durability: Cold forging dies are subject to cyclic loads and intense pressure. Materials with high wear resistance and toughness can significantly extend tool life, reducing downtime and overall production costs.
Precision and Consistency: Maintaining dimensional accuracy over multiple forging cycles is essential. High-quality die materials ensure that the geometry of the die remains intact, delivering consistently accurate parts.
Cost Efficiency: Although premium materials may carry a higher upfront cost, their durability and reduced maintenance needs often lead to long-term cost savings.
Using an inferior or poorly selected cold forging die material can lead to premature wear, dimensional inaccuracies, and even catastrophic die failure, which ultimately impacts production schedules and profitability.
Key Properties of an Ideal Cold Forging Die Material
When evaluating materials for cold forging dies, several critical properties must be considered:
1. Hardness
A primary requirement for any die material is high hardness. Harder materials resist wear and deformation under high stress. However, a balance must be struck; if the material is too hard, it may become brittle. This is why materials used in cold forging dies are often heat-treated to achieve an optimal hardness level while maintaining toughness.
2. Toughness
Toughness is the ability of a material to absorb energy and plastically deform without fracturing. Cold forging dies must endure repeated high-impact forces without cracking or chipping. A tough cold forging die material provides resilience against sudden loads and stress concentrations that occur during the forging process.
3. Wear Resistance
Die surfaces are in constant contact with the workpiece, leading to abrasion and wear. High wear resistance is essential for minimizing the frequency of die maintenance and replacement. Advanced alloys and surface treatments can greatly enhance this property, ensuring the longevity of the tool.
4. Machinability
Even the most durable material must be workable. The chosen cold forging die material should be easy to machine into precise shapes with smooth finishes. High machinability reduces production times and ensures the die can be manufactured within tight tolerances.
5. Thermal Stability
Although cold forging is performed at room temperature, the localized heating due to friction can affect the die. Materials with excellent thermal stability ensure that the mechanical properties remain consistent even during intermittent temperature spikes.
Common Cold Forging Die Materials
Several materials have proven effective in the cold forging industry. Among the most widely used are specialized tool steels. Here are some common options:
A2 Tool Steel
A2 tool steel is highly favored for its balanced properties. It offers excellent toughness, high wear resistance, and can be heat-treated to achieve desirable hardness levels. The fine-grain structure of A2 makes it ideal for precision cold forging applications, where dimensional stability is paramount.
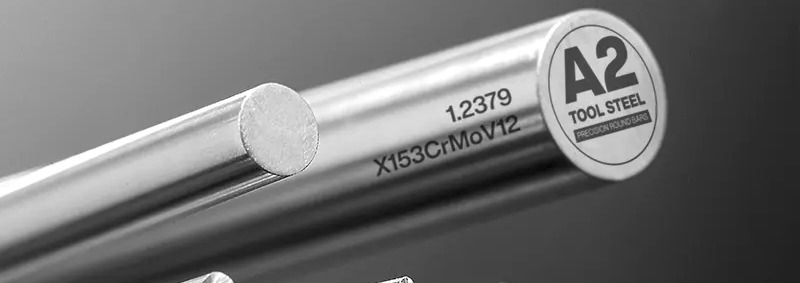
D2 Tool Steel
Known for its high wear resistance, D2 tool steel is another popular choice. Its high carbon and chromium content allow it to form a hard, wear-resistant surface. However, the higher hardness comes with slightly reduced toughness compared to A2, so its use is best suited to applications where abrasion is the primary concern.
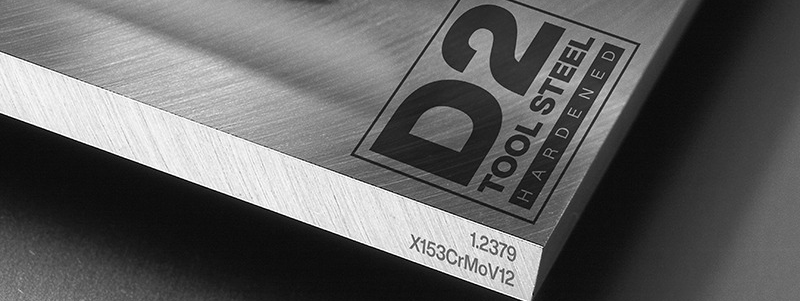
O1 Tool Steel
O1 tool steel is appreciated for its excellent machinability and moderate toughness. It is often used in scenarios where the complexity of the die design necessitates high precision machining. O1’s properties make it suitable for lower volume production or prototype forging applications where customization is critical.
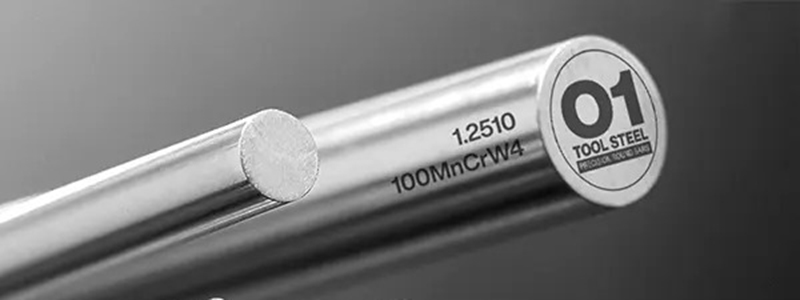
Powder Metallurgy Steels
Recent advances have also seen the use of powder metallurgy (PM) steels in cold forging. These materials offer uniform microstructures and excellent mechanical properties. PM steels can be engineered to achieve both high toughness and wear resistance, making them a competitive alternative to conventional tool steels.
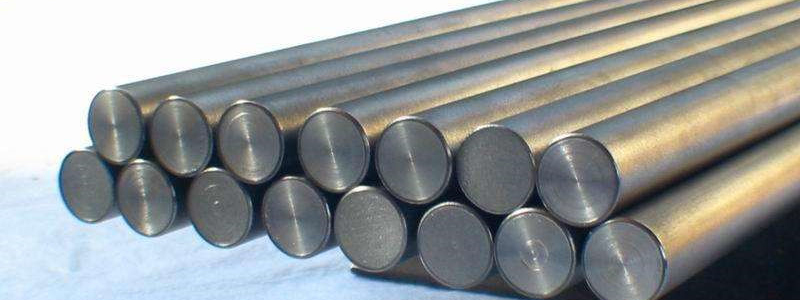
Heat Treatment and Surface Engineering
Once the base material is chosen, the next critical step is heat treatment. This process is crucial for optimizing the mechanical properties of the cold forging die material. Heat treatment processes, such as quenching and tempering, help achieve the required balance of hardness and toughness. In many cases, a secondary process like cryogenic treatment is also applied to reduce retained austenite and improve wear resistance further.
In addition to heat treatment, surface engineering techniques—such as nitriding, carburizing, or applying hard coatings—are employed to extend the life of the die. These processes form a hardened surface layer that offers superior resistance to friction and wear without compromising the toughness of the core material.
Challenges in Cold Forging and How the Right Material Helps
Cold forging operations are not without their challenges. Common issues include:
High Cycle Fatigue: Repeated high-stress cycles can lead to fatigue failure if the material isn’t sufficiently robust.
Abrasion and Surface Damage: Continuous contact with the workpiece can wear down the die surface, compromising part quality.
Thermal Stresses: Even at room temperature, localized heating can induce thermal stresses that may cause micro-cracks.
Choosing the correct cold forging die material can significantly mitigate these issues. For example, a material with superior toughness will better withstand high cycle fatigue, while one with excellent wear resistance will maintain surface integrity despite constant friction. Moreover, materials engineered for thermal stability ensure that even transient temperature fluctuations do not compromise the die’s performance.
Innovations and Future Trends
The landscape of cold forging is continuously evolving. Innovations in material science and manufacturing processes have led to the development of advanced alloys and composite materials that push the boundaries of performance. Some emerging trends include:
Nanostructured Alloys: These alloys are designed at the nanoscale to offer enhanced strength and wear resistance. They represent a promising frontier for next-generation cold forging die materials.
Hybrid Material Solutions: Combining different materials or incorporating surface coatings with traditional tool steels can provide a tailored approach that optimizes both core toughness and surface durability.
Sustainable Manufacturing: As industries move toward greener practices, there is an increasing focus on developing die materials that not only perform well but also reduce the overall environmental footprint of the manufacturing process.
By staying abreast of these trends, manufacturers can ensure that they are using the best available cold forging die material to meet the demands of modern production environments.
Conclusion
The selection of the right cold forging die material is paramount to the success of any cold forging operation. With the right balance of hardness, toughness, wear resistance, machinability, and thermal stability, manufacturers can achieve longer tool life, improved precision, and reduced production costs. Whether it’s the traditional A2, D2, or O1 tool steels or the newer powder metallurgy alloys, the key is to understand the specific requirements of your forging process and choose a material that meets those needs.
In a competitive manufacturing landscape, leveraging the best cold forging die material is more than just a technical decision—it’s a strategic one. It can lead to enhanced operational efficiency, better quality parts, and ultimately, a significant competitive edge in the market.
By investing in the right materials and staying informed about the latest innovations, companies can ensure that their cold forging processes remain at the cutting edge of technology and efficiency.
This detailed guide is intended to help industry professionals and decision-makers understand the complexities involved in selecting the optimal cold forging die material. We hope it serves as a useful resource in navigating the technical and economic challenges of modern cold forging operations.
Feel free to share your thoughts or contact us for further insights on optimizing your forging processes.